Laser Stereolithography: Precision in additive manufacturing
The Laser Stereolithography (SLS for short) is one of the most innovative processes in additive manufacturing. With its ability to create complex 3D structures with exceptional precision, it has established itself in areas such as prototyping, biomedicine and micromanufacturing. This process uses the power of light to polymerize materials layer by layer, thereby offering an alternative to traditional manufacturing techniques such as injection molding or CNC machining.
what is Laser Stereolithography?
The Laser Stereolithography is based on a photochemical process in which a laser beam specifically polymerizes light-curing plastics. Liquid photopolymer is converted into solid layers by the action of UV light. A three-dimensional object is gradually created through layer-by-layer curing.
The process differs from other additive manufacturing techniques such as laser sintering, in which powder is fused by a laser beam. While sintering requires high laser power, stereolithography requires comparatively less energy because polymerization is a chemical and not a thermal process.
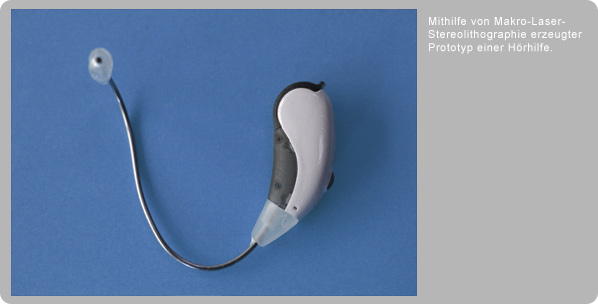
Macro-Laser Stereolithography: High precision for large objects
The Macro-Laser Stereolithography (SLS) is used primarily for larger objects in rapid prototyping. In the past, HeCd lasers with a wavelength of 325 nm were often used for this technique. However, the further development of laser technology has made solid-state lasers with 355 nm increasingly popular. These new lasers are more durable, more compact and more cost-effective.
By converting to more modern UV lasers, SLS machines can now produce objects with impressive precision. With layer thicknesses of up to 0.01 mm, delicate structures can be created with a size of up to 40 x 35 cm. Due to this technology, rapid prototyping has revolutionized the industry and is increasingly being used in series production.
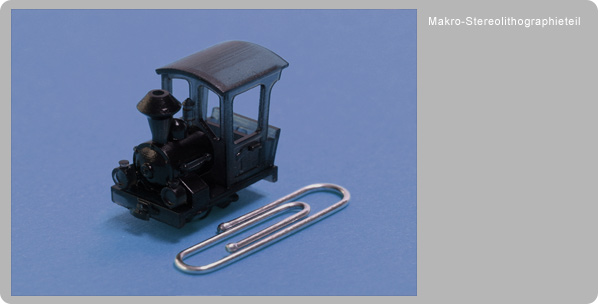
Micro-Laser Stereolithography: Structures in the sub-micrometer range
The Micro-Laser Stereolithography (µSLS) uses two-photon absorption, also known as two-photon polymerization. Short-pulse lasers with wavelengths of 1064 nm or 532 nm are used. This technique enables the creation of structures with a resolution in the sub-micrometer range through the non-linear process.
An outstanding example is the production of a chess piece in the µm range, which was realized at the Fraunhofer Institute ILT using our laser. This technology overcomes the diffraction limitation of the laser and enables a level of detail that is unattainable with other manufacturing processes.
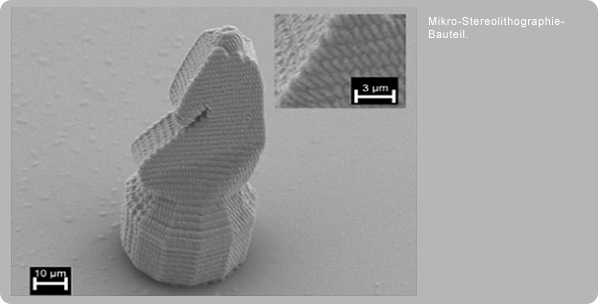
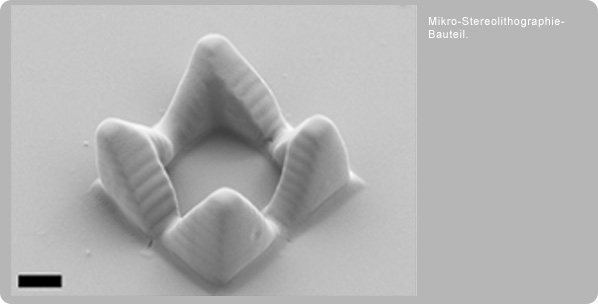
Applications of Laser Stereolithography
1. Rapid prototyping
The Laser Stereolithography is ideal for rapid prototyping and allows engineers and designers to quickly test and flexibly adapt concepts without having to rely on time-consuming traditional manufacturing methods.
2. Biomedicine
Micro-stereolithography offers exciting possibilities, especially in biomedicine. The smallest pumps, motors and support structures can be manufactured in the micrometer range. In addition, these structures serve as growth aids for cells and enable detailed research into cell interactions with artificially created protein structures.
3. Microfluidics
In microfluidics, a key technology for the development of lab-on-a-chip systems, µSLS is used to create precise channels and chambers. These structures are also essential for the precise analysis of very small amounts of liquid in medical and chemical applications.
4. Optoelectronics
In the field of optoelectronics, the Laser Stereolithography the production of miniaturized components such as optical lenses or holders for LEDs. In addition, this technology offers the possibility of creating high-precision structures that would not be possible with traditional methods.
Advantages of Laser Stereolithography
- Highest precision: The resolution extends into the sub-micrometer range.
- Versatility: Suitable for prototyping, biomedicine and series production.
- Efficiency: Fast production with minimal material waste.
- variety of materials: Can be used with various light-curing polymers.
- Design freedom: Complex geometries that would not be possible with traditional methods can be easily realized.
Challenges and future of Laser Stereolithography
Despite their advantages, there are also challenges. Selecting the right photopolymer and optimizing laser parameters are critical to success. In addition, some applications require post-processing to improve the mechanical properties of the finished object.
In the future, the further development of materials and laser technologies will Laser Stereolithography even more powerful. Improved resins and even more precise laser systems could expand the fields of application and create new possibilities in industry and medicine.
Conclusion
The Laser Stereolithography is a breakthrough technology that combines precision, versatility and efficiency in additive manufacturing. With applications ranging from prototyping to biomedicine to micromanufacturing, it has the potential to complement or replace traditional manufacturing methods in many areas. The continued development of this technology will only increase its importance in the future.